Les stocks pèsent pour plusieurs centaines de milliards d’euros dans les bilans financiers des entreprises françaises *. Sans compter que chaque m² mobilisé pour entreposer, est un espace perdu pour une mission pouvant servir la croissance.
Pour contrer cette problématique, un ingénieur japonais émet une idée : pourquoi ne pas produire à la demande ? À partir de cette idée, il bâtit toute une méthode complète de production agile : le JAT (Juste-à-temps) , un concept fondateur du TPS (Toyota Production System).
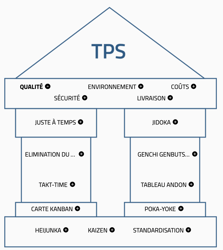
#1 Se démarquer avec la méthode du Juste-à-temps
La création de ce modèle révolutionnaire fait suite à un voyage aux États-Unis de Kiichiro Toyoda (fils de Sakichi Toyoda et créateur de Toyota Motor) et Taiichi Ohno (ingénieur au sein de la firme historique dédiée aux métiers à tisser), dans les années 50.
Ils émettent 3 constats :
- Le Japon ne produit pas d’automobiles.
- Les Américains ont une productivité 9 fois supérieure à celle des Japonais.
- Le Japon ne peut pas rivaliser en suivant le même modèle que Ford ou General Motors, à savoir : une production massive, adaptée à la taille de leur marché, en dépit des rebuts et des stocks.
Malgré ce contexte concurrentiel, le gouvernement japonais demande au groupe Toyota de débuter la production de véhicules automobiles. Pour répondre à ce défi, une réponse est possible :
« Produire juste ce dont on a besoin et le faire juste à temps ».
Ce qui sous-entend de fabriquer rapidement, d’éliminer les coûts annexes et diminuer les stocks en vendant rapidement des voitures à un prix moins élevé.
#2 Devenir agile
Le Juste-à-temps (JAT) s’articule autour des principes de Takt Time, de flux de production continu, de changement d’outils rapide, de logistique interne optimisée.
Il prend tout son sens pour répondre à notre mode de consommation contemporain. Face à des clients de plus en plus exigeants sur la qualité et les délais, des demandes en constante évolution et une concurrence ouverte au monde, la production en flux tendu prend tout son sens.
Dans son application, le JAT impose certaines règles :
- Tout d’abord, il nécessite une bonne connaissance des processus en place, soit une organisation exemplaire et une vue globale de chaque étape de la fabrication. Cette vision permet alors de freiner ou booster la production de chaque poste, en fonction des stocks et des capacités de chaque opérateur.
> le Kanban - Il est également essentiel d’anticiper les défaillances mécaniques ou humaines en engageant des contrôles continus, sur toute la chaîne de production et sur l’ensemble de ses maillons.
> le Jidoka - Le JAT impose aussi que l’on se débarrasse de ce qui pourrait encombrer ou perturber les opérateurs dans l’exécution de leur tâche.
> les 5S - Pour une application optimum, il convient d’identifier et de supprimer tous les facteurs de perte de temps, de gaspillage occasionné par les transports ou par les stocks, susceptible de ralentir le rythme de production.
> les MUDA - La formation est aussi une étape incontournable pour avoir des opérateurs performants, polyvalents, capables de s’adapter aux différentes variations de flux.
> Le Kaizen
Ces outils servent un objectif : éviter le gaspillage en produisant de la qualité, du premier coup.
#3 Engager ses partenaires
Mais appliquer le JAT, c’est étendre cette culture bien au-delà des murs de l’entreprise. En effet, une fois ces dispositifs mis en place, il faut engager toutes les parties prenantes afin d’instaurer une collaboration durable. C’est même un élément clé d'une méthode de JAT réellement pérenne.
Ainsi il convient d’appliquer les principes suivants :
- Mettre en place une relation de confiance avec ses fournisseurs, les accompagner dans leur apprentissage et leur pratique du TPS.
- Estimer les besoins en fonction d’une demande réelle et non-prévisionnelle.
- Privilégier des fournisseurs locaux afin de limiter les coûts, temps et risques nombreux liés aux transports.
- N’acheter que les matières premières utiles à la production, pour limiter les frais de stockage.
- Miser sur un réseau global fiable (transport, livraison). En effet, de ce facteur, dépendra l’ensemble de la production, influant inévitablement sur la satisfaction client.
Le JAT (Juste-à-temps) repose sur une organisation rationalisée de la production, en flux tiré, déclenchée par la demande.
Il répond à une première problématique : le coût et la gestion de l’entreposage.
Mais sa mise en place, engageant les fournisseurs, les collaborateurs, remettant en question le fonctionnement de votre entreprise peut provoquer des bénéfices allant bien au-delà d'une problématique de stock.
Si à votre tour, vous souhaitez découvrir et mettre en place des outils TPS vous pouvez :
- Télécharger notre livre blanc en cliquant sur le bandeau ci-dessous
- Être formés par des experts rompus à la pratique de cette méthode, Toyota Material Handling a développé une offre certifiante qui saura s’adapter aux besoins particuliers de votre entreprise. Pour en savoir plus sur la certification TPS de Toyota Material Handling, cliquez ici.
*https://www.datapowa.fr/blog/3/le-poids-des-stocks-en-france