À la recherche de l’équilibre entre la demande et la production, Toyota crée un nouvel outil Lean : la méthode Kanban.
Son rôle ? Servir le principe « d’amélioration continue » souhaité par le constructeur, en apportant une visibilité sur les stocks et en déclenchant la production, à la demande.
Mais cette définition ne saurait expliquer à elle seule la complexité du Kanban.
Sur quels principes repose-t-il ? Quel est son fonctionnement ? Pour quels résultats ?
Aujourd'hui, nous vous accompagnons dans la compréhension du Kanban.
Le Lean s’attache à faire grandir l’entreprise et les hommes qui la composent. Comment ? En conjuguant un système de production intelligent et une philosophie managériale basée sur le respect et l’amélioration continue.
Coûts de fabrication réduits, délais de production diminués, surproduction évitée et qualité optimisée sont les principaux résultats obtenus par Toyota, dès la création de cette méthode, au milieu du siècle dernier.
Les outils servant les objectifs du Lean sont nombreux (et complexes).
Le Kanban est l’un d’eux. Son objectif : donner de la visibilité sur les stocks pour produire à la demande.
Pourquoi Toyota a créé le Kanban ?
C’est au cours d’un voyage aux États-Unis que Kiichiro Toyoda prit connaissance de la méthode qui inspira le Kanban, utilisée dans les supermarchés depuis le début du 20ème siècle (1916).
Il put y observer deux points. Le premier était que les clients se servaient eux-mêmes directement sur les linéaires. Le second était que lorsque l’un deux se trouvait vide d’une référence, un bon de remplacement était automatiquement généré.
Kiichiro Toyoda adapta le concept pour l’usine automobile Toyota dans l’objectif d’améliorer la flexibilité et de réduire le niveau de stock.
Produire en « flux poussé », correspond à la capacité d’une entreprise à fabriquer en continu, sans considération pour la demande réelle. Surproduction, gaspillage, sollicitation inutile des opérateurs, augmentation des stocks… On constate très rapidement les limites de ce modèle.
Dans un contexte de production agile, Toyota va privilégier un système de « flux tiré », déclenché par la consommation.
On peut donc la définir comme un système permettant de partager l’information et de maîtriser visuellement le flux. Lorsqu’une anomalie est détectée, cette méthode permet également de stopper la production, plus facilement qu’en « flux poussé ». En cela, elle fait écho au Jidoka, pilier du Lean.
Comment fonctionne le Kanban en Lean ?
Les besoins en matière de fabrication et de manutention sont matérialisés par des cartes (également appelées Cartes Kanban).
Sur ces dernières, sont indiquées des informations propres aux produits demandés, attachées aux cartons ou palettes contenant les marchandises destinées aux postes situés en aval sur le schéma suivant.
Celles-ci permettent de signaler au fournisseur que certains lots sont entamés et qu’un réapprovisionnement est nécessaire. Ainsi, l’entreprise n’émet de demande de livraison en matière première, si et seulement s’il y a de la demande. À l’inverse, s’il n’y a pas de demande, les lots ne sont pas entamés, les commandes aux fournisseurs sont diminuées.
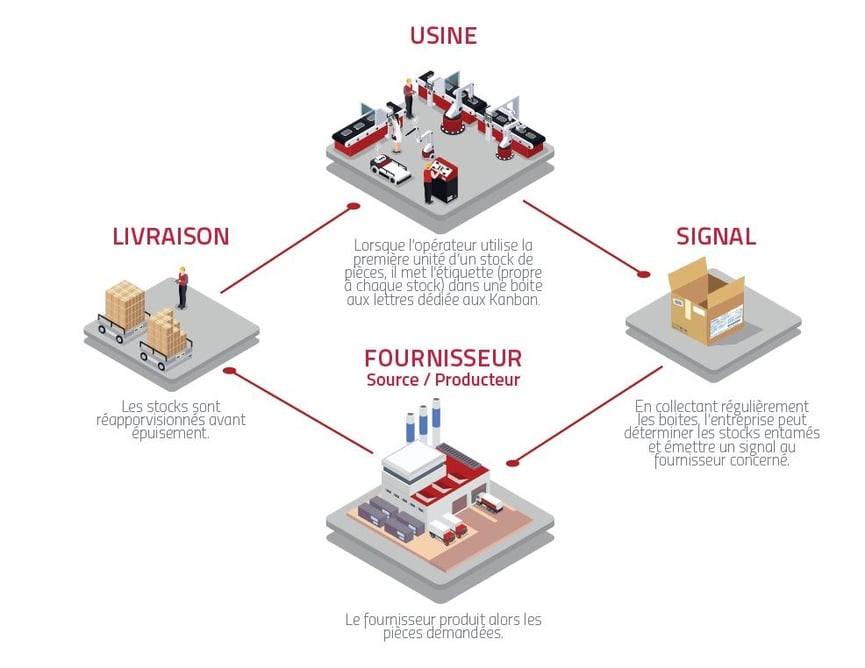
La particularité de cette méthode, c’est qu’elle peut être applicable également en interne. Sur une production, composée de plusieurs postes successifs, les opérateurs en bout de chaîne manifestent leurs besoins et sollicitent le travail des postes en amont dans la chaîne. Ainsi, chaque opérateur produit le juste nécessaire.
La réception de Cartes Kanbans en interne, informe les équipes en amont que le stock se vide progressivement.
Dans une méthodologie traditionnelle, on a tendance à produire, tant qu’il y a de la matière brute ou/et que la hiérarchie en donne l’ordre.
Avec la visualisation du Kanban, le flux s’adapte directement à la demande, à l’intérieur comme à l’extérieur (fournisseurs) de l’entreprise.
Dans la réalité, il sert également d'autres intérêts, pour les opérateurs :
#1 Visualisation
Jaugeant la production, il met en évidence le workflow (flux des tâches) et permet d’anticiper sur les besoins à venir, sans attendre le briefing d’un supérieur. Ainsi, il accorde une certaine forme d’autonomie aux opérateurs (Team Members).
#2 Limitation des tâches
Dans le Kanban, le nombre de tâches est limité. Lorsqu’une d’elles est réalisée, elle disparaît, au profit d’une nouvelle. Le volume d’actions reste constant et toujours adapté aux capacités de l’opérateur. Grâce au nombre de cartes Kanban en circulation, les phases de surcapacité ou, au contraire, d’inactivité et donc de Muri sont éliminées.
#3 Identification des leviers d’optimisation
Cet affichage met en évidence des anomalies régulières. Cette technique produit les data nécessaires pour identifier des goulots d’étranglement, un fonctionnement inadéquat. Elle permet ainsi de penser d’éventuels leviers d’optimisation.
Quels sont les avantages du Kanban Toyota pour l’entreprise ?
Outil au service du Lean, il permet de prévenir de certains Muda (7 typologies de gaspillage) comme la surproduction, le temps d’attente ou la gestion de stocks inutiles.
De plus, cette méthodologie est très flexible. Elle permet de freiner ou d’arrêter la production en cas d’anomalie, avant la non-conformité. Elle sert ainsi une autre notion du Lean : le Jidoka.
Enfin, elle implique et prend en compte les capacités de l’opérateur, lui donnant la possibilité d’intervenir directement sur un problème et de ne pas produire inutilement.
On a tendance à associer la méthodologie Kanban au secteur industriel.
Mais libre à tous les autres domaines de se l’approprier et de profiter de ses avantages.
Gardons à l’esprit que le Kanban reste un outil Lean.
Sa seule application permet d’obtenir des résultats très positifs, grâce à une prise de conscience des stocks et de l'ensemble des besoins de la chaîne de production.
Mais son réel potentiel s’exprime pleinement dans une démarche d’amélioration continue et de mise en place d’une culture globale du Lean Management, au sein de l’entreprise.
De ce fait, une entreprise qui souhaite entreprendre une transformation profonde, mérite un accompagnement adapté.
Si à votre tour, vous souhaitez découvrir et mettre en place des outils TPS vous pouvez :
- Télécharger notre livre blanc en cliquant sur le bandeau ci-dessous.
- Être formés par des experts rompus à la pratique de cette méthode, Toyota Material Handling a développé une offre certifiante qui saura s’adapter aux besoins particuliers de votre entreprise. Pour en savoir plus sur la certification TPS de Toyota Material Handling, cliquez ici.